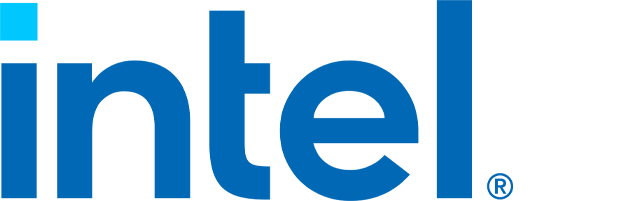
In 1965, Intel co-founder Gordon Moore made a stunning observation: The number of transistors per square inch on integrated circuits had doubled every 18 months since their invention. He predicted the trend would continue into the foreseeable future—and it generally has. A billion transistors now fit on a chip the size of a pea.
Challenge:
In a complex, fast-growth industry, Intel must continuously innovate while controlling costs and maintaining quality.
Industry:
Information Technology
Solution:
SAFe®, Agile and Lean
Results:
- MVE delivered 65% more products with the same capacity.
- Improved Commit-to-Accept ratios from 74% to +90%.
- Everything is visible to everyone.
- Scope change reduced to less than 5%.
Best Practices:
- Choose the right RTEs – Intel found that effective RTEs have a combination of technical background and a deeper Agile mindset/experience
- Train the Leaders – Business owners and Train Management should be required to attend SAFe training. It is critical that the leaders speak for the transformation, act as role models, and reinforce direction within the organization. Leverage advocates in the organization whenever possible.
- Always end with Inspect & Adapt – Just get started and then learn and adapt. Favor “progress over perfection.”
- Keep it Simple – Don’t overcomplicate the process, and bring things back to the basics of Agile and Lean.
Introduction
Intel has been integral in pushing that pace of growth in the marketplace. Today, the company employs more than 100,000 people globally and reports net revenue of $59.4 billion.
But like most enterprises, as it continuously innovates and expands, Intel must balance cost control while maintaining high quality.
“With the complexity and number of the products skyrocketing, if we didn’t adjust or adapt, other than adding more people, Moore’s Law would crush us,” says Allen Ringel, Lean & Agile Transformation Leader, Intel.
Agile at Enterprise Scale
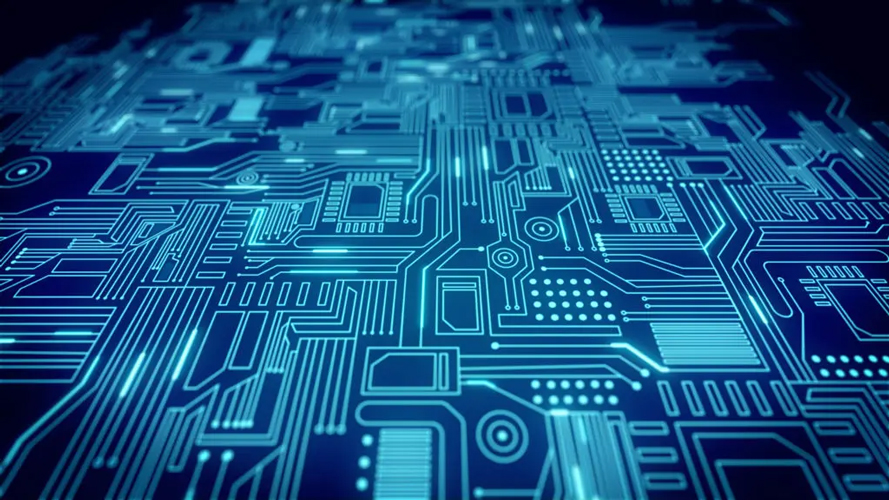
Intel’s Manufacturing Development Organization (MDO) division tests and validates Intel solutions, producing over two million lines of code every two weeks. In an effort to deliver more value, MDO began to adopt Lean-Agile practices in 2005, and by 2012 had small pockets of Scrum and a homegrown solution for scaling Scrum.
“We found the Agile approach attractive because it turns the Iron Triangle on its head,” Ringel says. “Features are negotiable but time, cost, and quality are not.”
Yet as more people and divisions were folded into MDO, Intel found it increasingly difficult to scale Scrum. Thus, a team of about 15 people tasked with driving Lean-Agile at Intel looked at industry frameworks for ways to scale more effectively.
In 2013, MDO discovered the Scaled Agile Framework® (SAFe®), which provided clear structure and roles for taking the company into the next phase of Agile. SAFe also aligned well with the company’s broader Lean approach as a learning organization focused on continuous improvement and waste elimination.
“In an organization as large as MDO we needed to standardize the planning and execution process we use to work together to deliver value,” Ringel says. “When we encountered SAFe it provided a proven, public framework, with well-defined roles and artifacts for applying Lean and Agile at the enterprise level.”
Those 15 Lean-Agile leaders prepared for the implementation by attending the SAFe Program Consultant (SPC) Certification training. After mapping the roles, principles, practices & tools to back to what currently existed in the organization, they had essentially created a trail through the forest with a visible plan for implementation. Then they jumped in with both feet.
Leading up to the first Program Increment (PI) planning event, Intel trained more than 1,500 people. Over the course of eight weeks, they launched eight Agile Release Trains (ARTs) with 170 Scrum teams—with Christmas and New Year’s in the middle. To ease the transition, the 15 Intel Lean-Agile coaches were embedded at the 14 different sites with MDO teams to answer questions and provide guidance.
At Intel, executive backing proved critical to the success of the rollout. Mohsen Fazlian, General Manager of the division, created a shared vision by communicating clearly about the reasons for adopting SAFe and scaling Agile. Intel also reinforced Scrum rules for teams to be properly sized, co-located, 100% committed, and cross-functional. Where co-location was not possible & budgets allowed, Intel brought together people in person for at least the first planning event.
That first PI, admittedly, demanded considerably more effort than subsequent events. Yet, the ability to see immediate value spurred momentum. “The planning events were essential for teams to align at the train level while highlighting dependencies and allowing risk mitigation early on,” Ringel says.
Intel made a few enhancements to the typical SAFe deployment. They digitized the program board so they could see everything on a dashboard at all times and identify efforts quickly as progressing normally or abnormally. Lean-Agile leaders guided managers in looking at abnormal areas from a new perspective. If something turned red on the virtual program board, instead of managers saying, “Fix this,” they ask, “How can I help?”
Training 2,000 Over Three Months
Fast forward to 2017. Intel has grown Lean-Agile practices at a pace that rivals Moore’s Law. The well-defined roles and terminology within SAFe serve as essential signposts for those new to the Framework.
The structure has kept the trains on track as the organization continuously expands. A merger with another group—now combined under the name Manufacturing Value Engineering (MVE)—nearly doubled the size of the organization.
To fold in the new division, MVE trained nearly 2,000 people over three months and immediately organized them into trains. While the change came as a bit of a shock to some, the rapid integration enabled people to participate in the Agile system while trainers consistently communicated the value of the change, helping people experience it first hand and embrace their roles with the new way of working.
“We all feel part of a bigger thing and speak a common language that everyone understands,” Ringel says. “There’s clarity in the model we work in, which has definitely been something people latch on to.”
Ringel says that Intel has settled on an acceptable ratio of coaches to employees: 1:200-250. “We have shown management that we can deliver value with half a percent of the organization as transformation leaders,” he says.
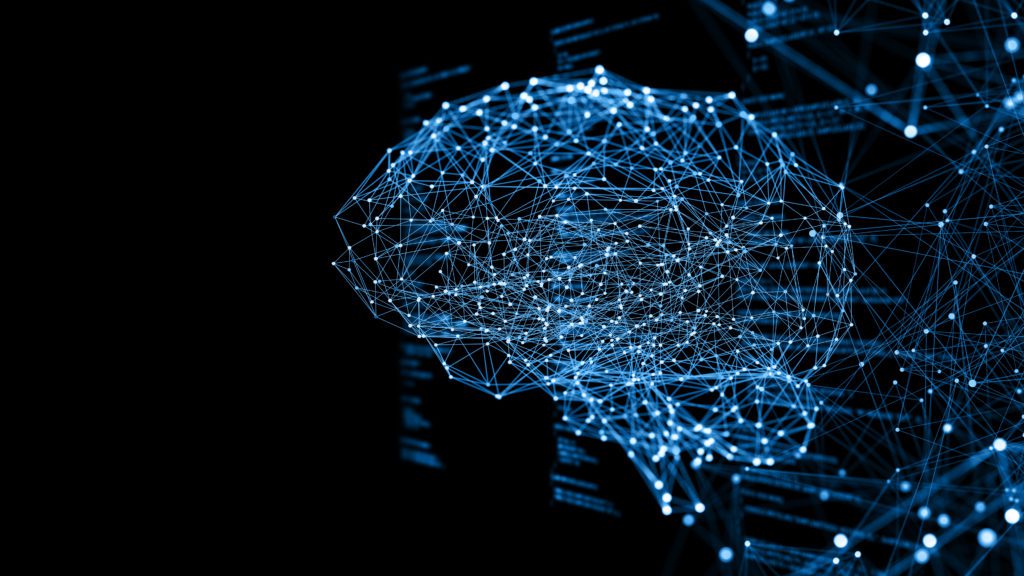
One of the Largest Reported SAFe Deployment
Today, MVE has over 440 Scrums organized into 35 ARTs, including software and hardware engineers. MVE continues to widen the circle and is frequently consulted by organizations throughout Intel. Adjacent organizations at Intel interested in MVE’s success have enlisted MVE to help with scaling Agile, leading to eight additional ARTs in partner organizations. In fact, Intel’s effort is one of the largest publicly reported SAFe deployment based on number of ARTs.
While scaling has not been easy, it has been worth it. The impact of these efforts ripples across the company.
Increased Product Variants
- Helped MVE to delivered 65% more product variants
Strong Performance-to-Schedule Discipline
- Capacity-based planning and cadence provides a heartbeat and prevents schedule slips
- Customers and upper management are changing their behaviors to protect the cadence set by Program Increments
- Commit-to-Accept ratios improved from 74% to +90%
- MVE minimized scope change in Program Increments to less than 5%
Increased Transparency & Visibility
- The company identified bugs, impediments, weak tools and poor engineering habits
- Transparency is invaluable and everything is visible to everyone
- Communication & conversations are more valuable than tracking indicators in a tool
- MVE now has a strong community with a common language
Institutionalized Process
- Teams have demanded adherence when the environment becomes chaotic
Ultimately, Intel’s Lean-Agile efforts help it maintain the industry’s rapid rate of growth.
“Lean & Agile help us deliver more products without adding more people, so we can stay competitive and keep up with Moore’s Law,” Ringel says.
Share:
Back to: All Case Studies
Suggested Case Study:
Deutsche Bhan