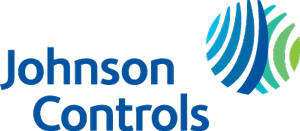
“SAFe brings so much more engagement, which has really been key for all parties. I wouldn’t want to do it any other way.”
—Rajbir Bal, Program Manager, Access Control
Challenge:
JCI’s access control division needed to improve coordination among firmware and software teams across three locations with the goals of improving time-to-market, quality, and engagement.
Industry:
Information Technology
Solution:
SAFe®
Results:
- The division releases at least 2-4X more frequently than before
- JCI reduced the size of its bug backlog by at least 3X
- Access control delivers on its commitments 100 percent of the time
- Customers/stakeholders appreciate the chance to provide feedback during the process—instead of at the end
Best Practices:
- Get help – Especially early on, partner with a consultant
- Train leadership – JCI trained resource managers, product management, and directors to get buy-in before moving forward
- Train SPCs – They serve as change agents and coaches
- Follow progress – JCI used automated Agile dashboards in Team Foundation Server
The partner that made it happen:
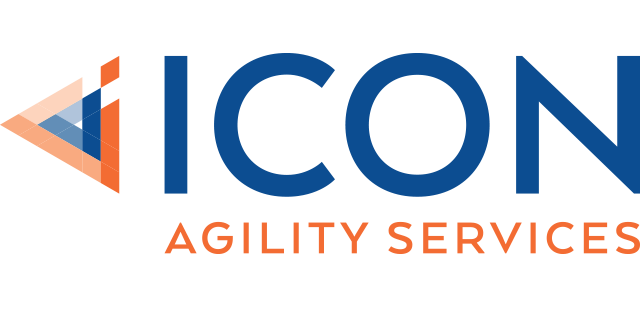
Introduction
Johnson Controls Inc. (JCI), a global diversified technology leader, serves customers in more than 150 countries and reports $30 billion in annual revenue. The company’s access control division develops systems to help buildings achieve maximum security while increasing efficiency and lowering costs.
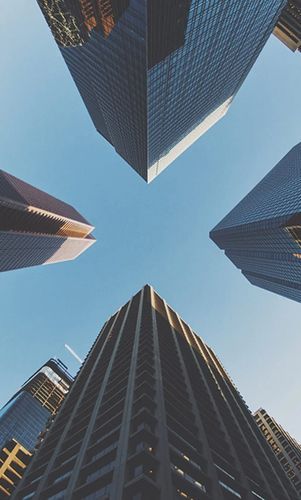
Developing access control systems demands that firmware and software teams work together to deliver on a coordinated schedule. At JCI, those teams are spread across Southern California, Milwaukee, and India.
In 2014, the division began an effort targeted at improving time-to-market and the predictability of releases. They also sought to identify quality issues sooner, increase transparency, and raise team engagement.
“We were having very little success at agility planning, predicting releases and committing to and delivering on the timeline,” explained David Richter, Director of Engineering, Access Control. “We wanted to increase our flexibility and ability to react to change, and to react to our customer’s needs in a positive and respectful manner.”
But Richter and other change agents knew they would have to contend with several roadblocks along the path to SAFe transformation:
- Changing the established paradigm of working in waterfall
- Aligning teams in three disparate locations
Taking the SAFe route
JCI identified the Scaled Agile Framework® (SAFe®) as the most promising route for instilling lasting Lean-Agile practices.
“SAFe brought all the practices for us to start and then learn and adapt as we go,” said Rajbir Bal, Program Manager, Access Control. “It also forced us to have tough discussions early and throughout development—versus down the road when we got close to release.”
To gain leadership backing, the Director of Engineering gave decision-makers clear reasons for deploying SAFe and the expected outcomes. Concurrently, Scaled Agile Gold Partner Icon Agility Services trained leaders in Leading SAFe® so they would fully understand the Framework. This worked well as change agents succeeded in securing executive backing.
They followed with Leading SAFe® for directors, product managers, and resource managers, bringing together 15 individuals from California, Milwaukee, and India. Next, they defined the structure of the various teams that would begin the first Agile Release Train (ART), and put all team members through SAFe® for Teams training.
Two individuals, including Bal, earned certification as SAFe® Program Consultants (SPCs) in order to serve as change agents and coaches. Following certification, they became authorized to deliver SAFe® Scrum Master, SAFe for Teams, and SAFe® for Product Owner/Product Manager training.
In addition to Bal, other coaches included engineering managers and the director of engineering, while Scrum Masters became coaches at the team level. When it was apparent that Scrum Masters and Product Owners had an overlap of responsibility, or at least their understanding of it, Bal brought them together in one location for a custom Product Owner/Scrum Master workshop to clarify roles and responsibilities.
Navigating the path to alignment
In 2015, JCI launched its first ART at a Program Increment (PI) Planning meeting with about 100 people and followed Essential SAFe. Bal and others knew they were taking the first steps toward progress, however, early planning events felt chaotic.
“The first two PIs were not fun and we did not come out with committed plans,” Bal said. “Some features were not well defined, people were not clear on the process, and we needed more time to break down user stories.”
Bal attributes the discord to a couple of factors. The company included some user interface teams in that first ART, but not others, which caused misalignment. Geographic distribution also created challenges.
For more cohesive teams, they tried several approaches. First, they brought representatives from India to present on behalf of their teams. However, in doing so, they lacked the voices of those not in attendance.
Instead, they decided to start concurrent planning in the U.S. and India, with India beginning 12 hours ahead due to the time zone differences. As teams in India complete their planning days, those in the U.S. come in early to overlap with them. The Indian teams present their planning via videoconference. The same goes for day two of planning. American teams presented in what was the evening for their Indian counterparts.
Richter notes that, in those early months, JCI attempted to modify the Framework. Only some teams attended training and the company followed three-week sprints. “We tried to make changes to SAFe, but that was a disaster,” he said. “After that experience, we then started following SAFe exactly.”
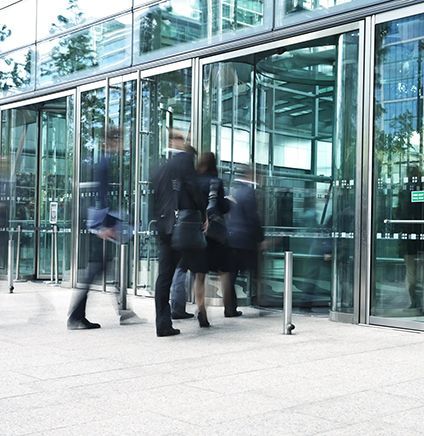
Many people also insisted on continuing lengthy documentation of functional and design specs, after 50 years of following this practice. But that changed over several PIs. “We realized that documentation is not adding value,” Bal said. “Instead, we switched more to flow diagrams and writing code versus paragraph after paragraph of specs.”
With these tweaks, subsequent PIs progressed more smoothly as everyone became accustomed to the ceremonies and practices of SAFe. They made better use of their time at PI planning events. By the third PI, all teams also joined the train.
Over time, JCI found it more feasible to modify the framework to its own processes. In the access control division, developers must follow a specific process. They found that SAFe allowed them to implement Lean-Agile methods that worked in conjunction with these required processes. Other modifications included concurrent planning for India and the U.S., and face-to-face meetings between Product Owners and Scrum Masters to walk through the features radiator.
Acting like ‘One Big Team’
Richter and Bal saw a number of positive outcomes emerge during the transformation:
- Increased ownership – Entire teams committed to goals in PI planning and delivered on those goals
- Less technical debt – Issues were identified earlier in development, which allowed for course corrections along the way, instead of at the end of development
- Greater participation – All levels joined in, including business partners and architecture
- Earlier decisions – Using the Lean Startup Cycle, they make go/no-go decisions sooner in the cycle than they had before practicing SAFe
- More automation – Automation reduced the overhead of testing and corrects quality issues earlier
- Enhanced transparency – People bring up issues sooner, rather than at the end of a PI
- Greater teamwork – Inter-team collaboration improved as well, with individuals reaching out to help others when needed
“We started acting like one big team, instead of a bunch of teams of teams,” Bal said. “We saw more engagement at all levels.”
Driving time-to-market, quality, predictability
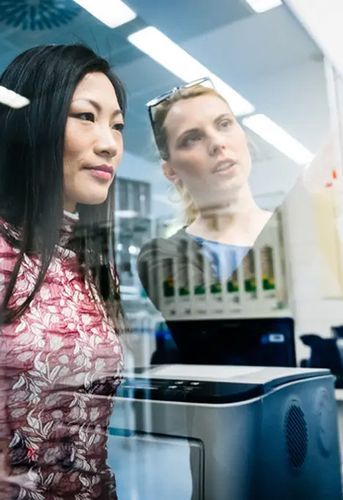
After early growing pains, JCI began seeing the results of its efforts:
- Faster time-to-market – The division releases at least 2-4X more frequently than before
- Higher quality – JCI reduced the size of its bug backlog by at 3 times
- Predictability – Access control delivers on its commitments 100 percent of the time
- Customer satisfaction – Customers appreciate the chance to provide feedback during the process—instead of at the end
“This wasn’t an easy process for us,” Bal said. “It takes time getting everyone jelling PI over PI. But SAFe brings so much more engagement, which has really been key for all parties. I wouldn’t want to do it any other way.”
For more details on JCI’s Essential SAFe implementation, download the supplemental PowerPoint presentation.
Share:
Back to: All Case Studies
Suggested Case Study:
Deutsche Bhan